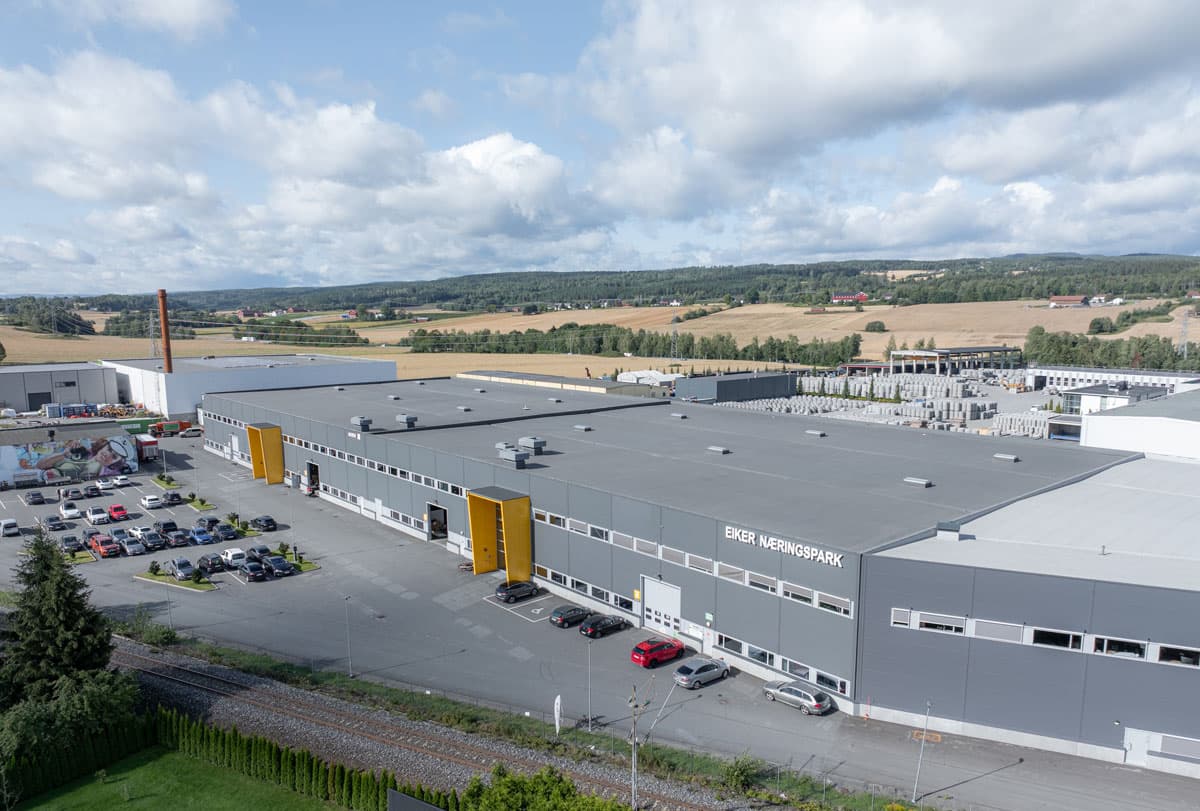
Mylna Sport optimizes its warehouse management
The project for Mylna Sport was a successful and well-coordinated effort that involved moving the head office and warehouse from Mjøndalen to Hokksund. By consolidating the goods, which were previously spread across several smaller warehouses, Mylna Sport was able to streamline its warehouse management.
A need to consolidate its goods in one single warehouse.
Mylna Sport is a major wholesaler of fitness equipment, including being a supplier to gyms. Mylna Sport was relocating its headquarters and warehouse from Mjøndalen to Hokksund and needed to consolidate its goods, which had previously been spread across several smaller warehouses in the area.
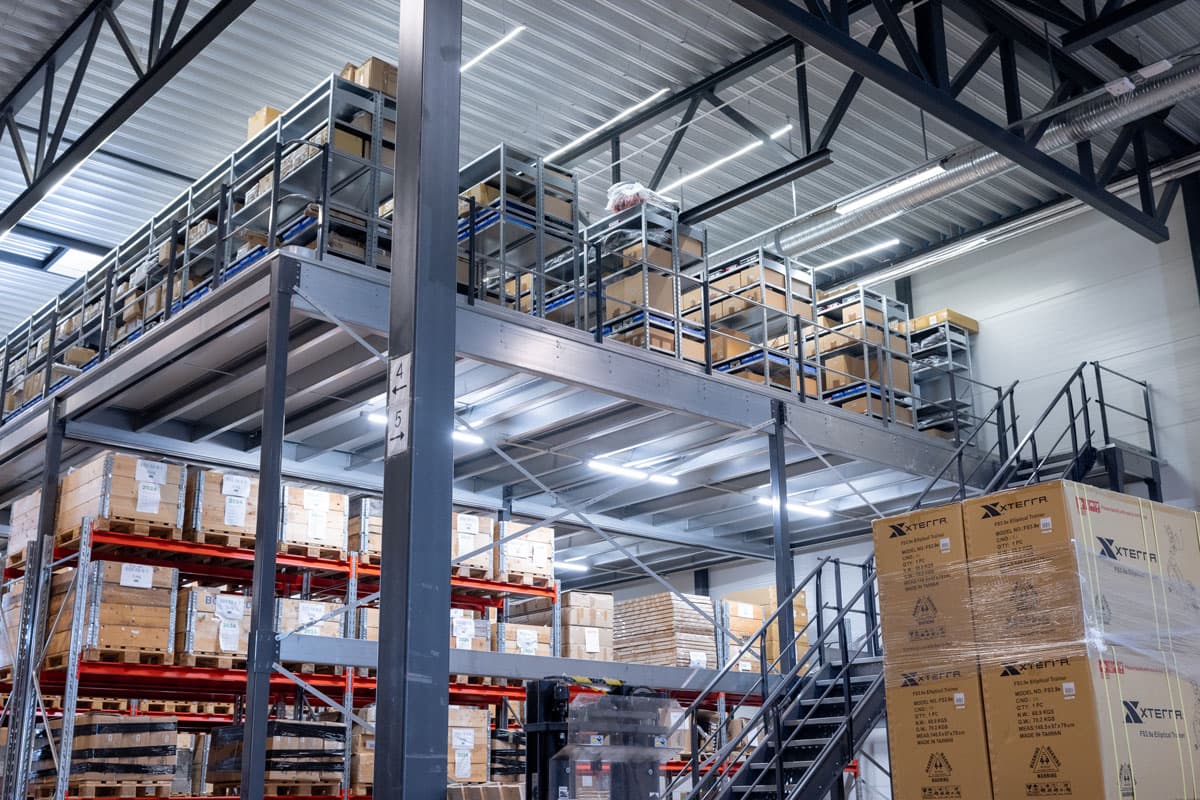
Warehouse solution based on the customer's needs
The big challenge was the mix of products, including rowing machines, treadmills, weights, and kettlebells. These are items that are very difficult to store efficiently – and they can be heavy.
BLS was involved early in the process over several years and presented solution proposals to demonstrate how we could meet the customer's needs in the new warehouse they were considering renting. Once the lease agreement was finalized, we worked closely with the customer to design the exact warehouse that would suit their mix of products.
"BLS has been actively involved in the process from the very beginning, providing several solution proposals tailored to our product groups in order to achieve an efficient warehouse."
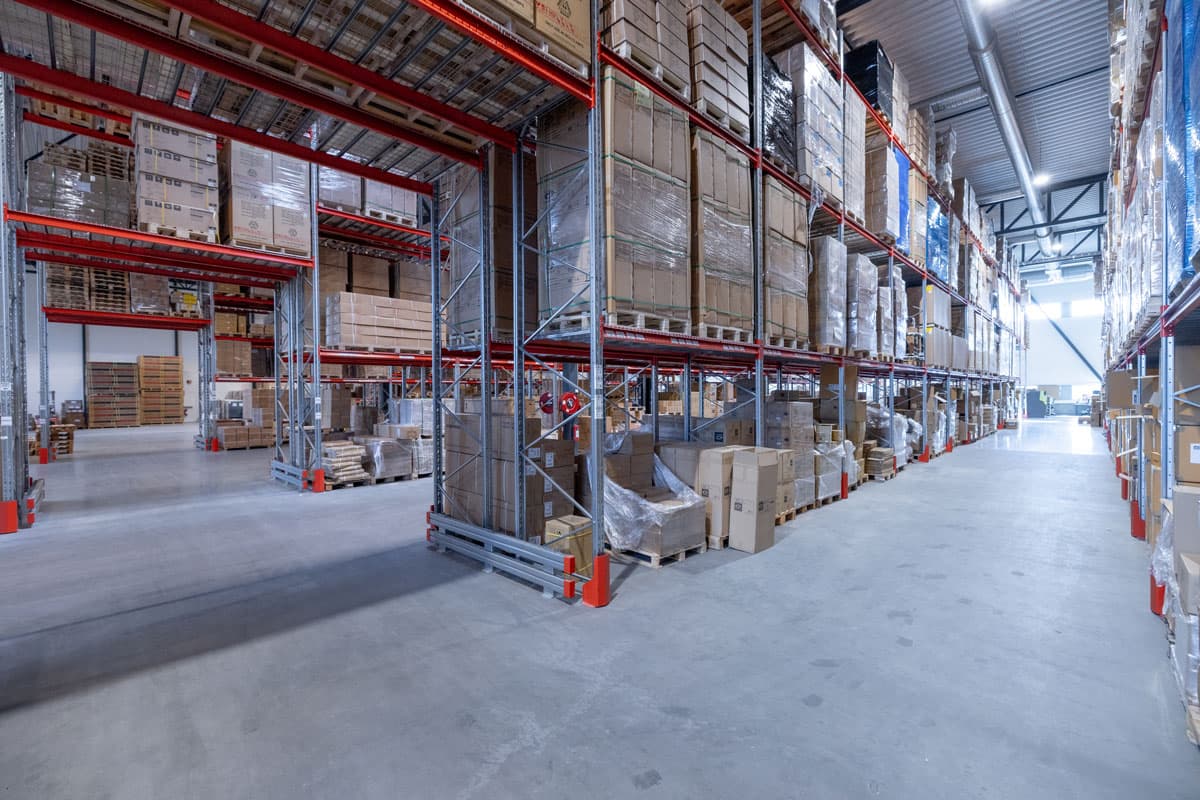
About 3,000 pallet spaces.
The new warehouse was actually already too small on paper, so we needed to be smart about it.
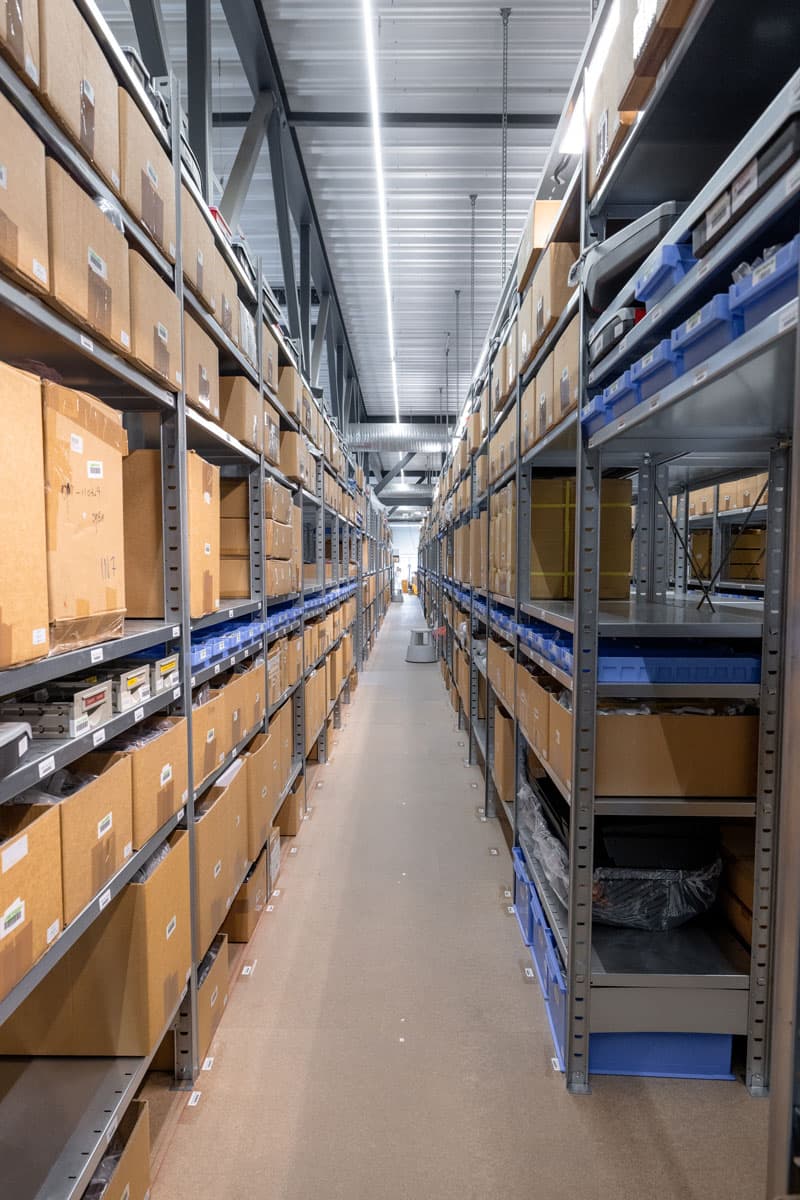
A 400 m² freestanding mezzanine system
A large spare parts warehouse also needed to be accommodated, and the solution was to build a 400 m² freestanding mezzanine system with 6 meters of clearance below. This allowed us to store all spare parts on pallet racking beneath the small parts, which were distributed across nearly 2000 shelving meters of Metro small parts shelving.
Close collaboration was necessary to tailor each shelving location to the correct height, and a great deal of work was required from the team at Mylna to simultaneously reduce the number of spare parts from their previous location.
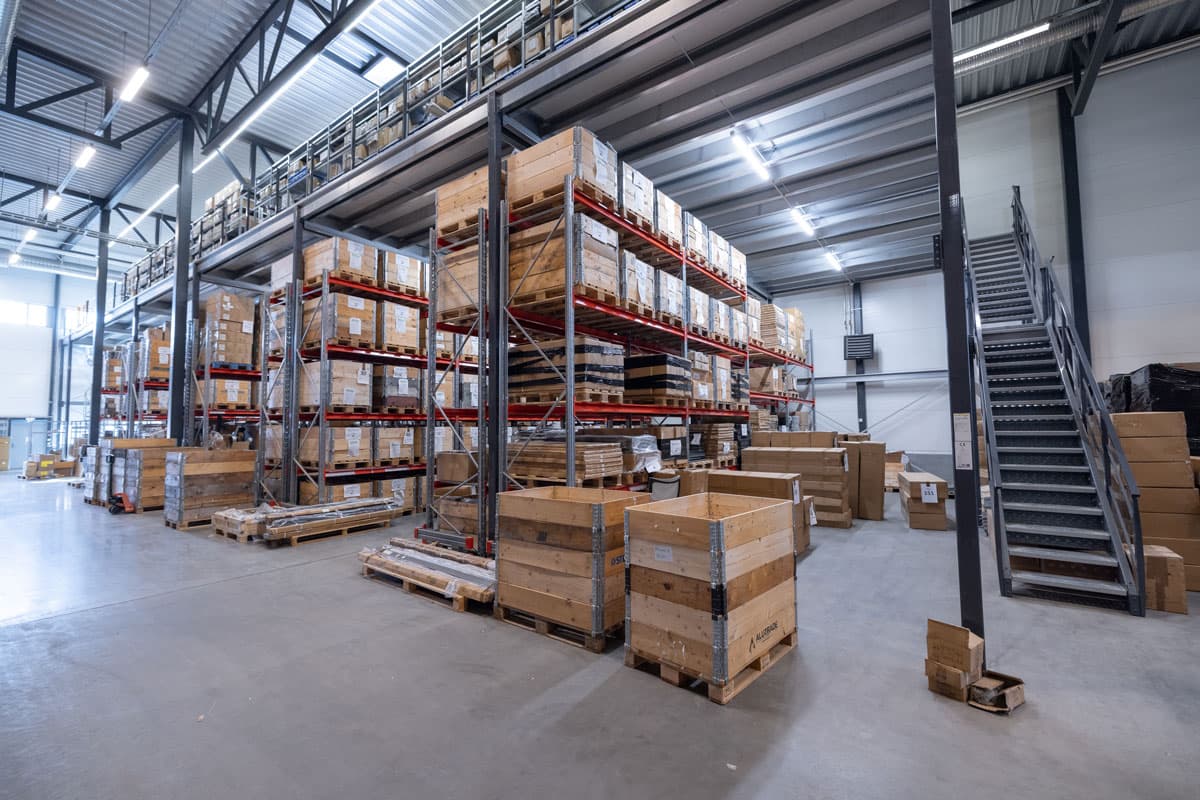
An already full warehouse required precise planning
An additional challenge that BLS took on without hesitation was that the warehouse where we were to install the shelving had already been filled with goods. This required careful planning, with the project manager and customer working side by side every day to complete the new racking and move the goods. Despite this, the process went smoothly, and we were able to install the entire system even faster than originally estimated.
“The installation team worked quickly, side by side with us in a warehouse that was already in operation. The process went seamlessly, they quickly adapted to any changes, and we were extremely satisfied with the result.”
Curious about how we can help you?
Do you have questions, concerns, or just want to say hello? Whatever it may be, we promise to do our best to assist you. Fill out the form with your details, and we’ll get back to you shortly.
Sustainable warehouse racking
Do you want to optimise your company’s space with smart warehouse equipment? Welcome to BLS. We don’t just offer a wide and well-thought-out range of warehouse systems and storage solutions – we also create solutions that make a real difference. Each warehouse system has been carefully designed and manufactured to meet and exceed all applicable requirements and standards. Manufacturing takes place in our own factory, located in the heart of Småland.
BLS is with you from day one
Choosing a new storage system, or updating an existing one, involves making many decisions, meeting deadlines and investing money, time and know-how. Let us apply our end-to-end approach. We’ll help you take the right decisions from the very start and make sure everything is done on time, on budget and as specified.